The cables come in different types and sizes, which makes it possible to supply electricity…
Parts of an electrical cable
Among the parts of an electrical cable, there are four different layers. The conductor, which channels the electrical flow, and an insulation containing this electrical flow in the conductor. In addition, parts of an electrical cable can incorporate other auxiliary elements that guarantee their longevity.
WHAT ARE THE PARTS OF AN ELECTRICAL CABLE?
1. CABLE CONDUCTOR
The first of the parts of an electrical cable that we highlight is the conductor. This is where the electrical current is actually transmitted, and copper is generally the most commonly used material.
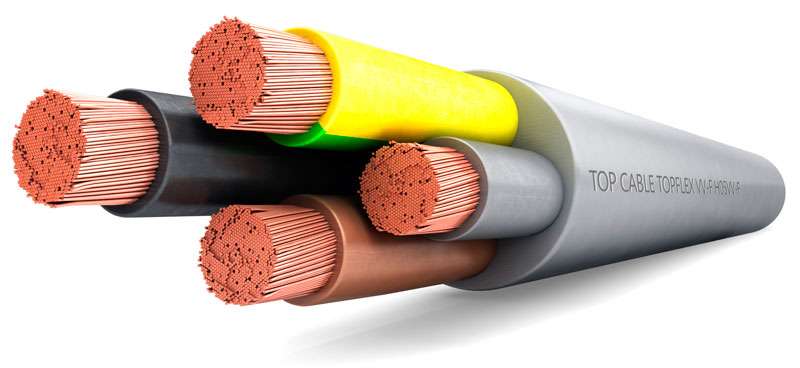
In some cases, aluminium conductors are also used, despite the fact that this metal is 60% worse conductor than copper (at the same cross-section it has more losses due to the Joule heating). In practice, aluminium is used almost exclusively for power transmission cables in electrical distribution networks (electricity companies).
There are two sizing criteria for copper conductors: the North American criterion and the European criterion. In the North American sizing (AWG), conductors are defined by specifying a number of wires and a diameter of each wire. In the European sizing (mm2), conductors are defined by specifying the maximum conductor resistance (Ω/km). You can consult the conversion table between both criteria in this post. Solid or flexible conductors are defined by specifying the minimum number of wires or the maximum diameter of the wires that make up the conductor. In addition, the actual geometric cross-sections are somewhat smaller than those indicated as nominal.
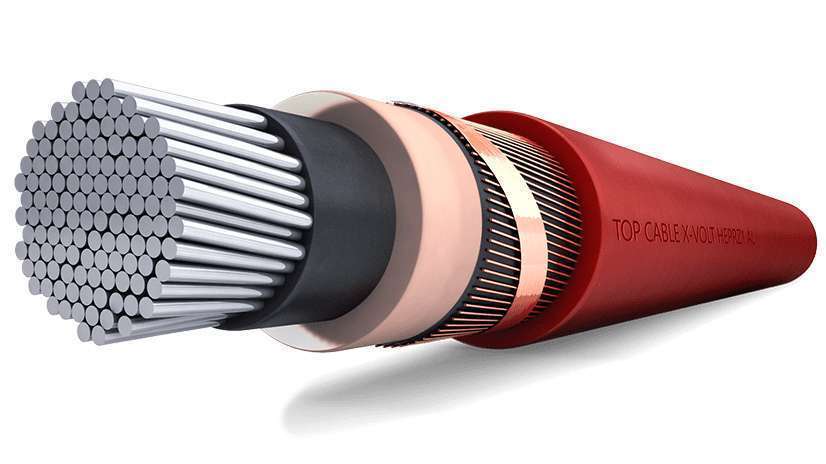
1.1 TYPES OF ELECTRICAL CONDUCTORS
There are a wide variety of options among electrical conductors and depending on the type, as parts of an electrical cable, determines the characteristics and the application that can be given to the product.
COPPER CONDUCTOR
This is the most common material in conductors, as it optimises the transport of electricity to the maximum and allows it to flow in the most optimal way. It is used in all types of installations, from residential installations to the industrial sector, or from electrical equipment to household appliances.
ALUMINIUM CONDUCTOR
Offer a lower energy conductivity (40% less). They are made up of one or more small wires which, when joined together, make up the aluminium conductor. Although we have highlighted the lower conductivity of aluminium, a positive aspect compared to copper is its weight, 70% less.
BRIDE CONDUCTOR
These are pairs of cables intertwined to cancel out electrical interference from external sources and crosstalk from adjacent cables. Their characteristics also allow for more reliable data transfer.
ARMOURED CONDUCTOR
It consists of one or more insulated conductors that are covered by a common conductive layer. This coating acts as a Faraday cage, preventing the coupling of noise or other interference between the environment and the conductor in a bidirectional manner.
RIBBON CONDUCTOR
Consist of a series of cables laid in parallel.
You can consult more types of electrical conductors here.
2. CABLE INSULATION
Insulation is the second of the parts of an electrical cable that we would like to highlight. In this case, it is the layer of polymer, plastic or elastomer that surrounds the conductor and insulates it from external contacts.
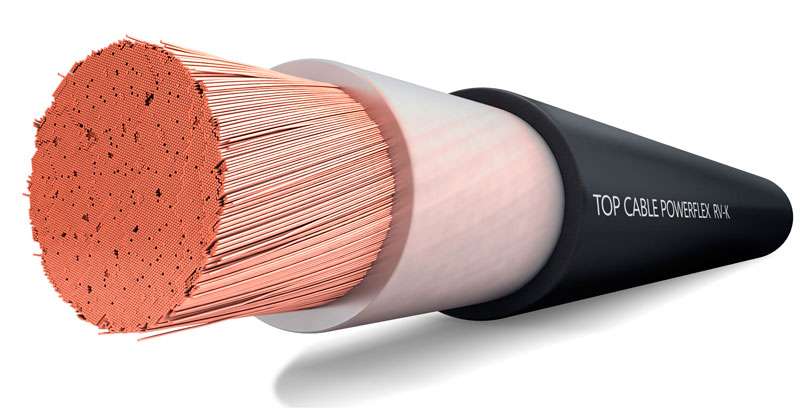
There are thermoplastic and thermosetting insulations. The first one are those in which the material applied does not undergo chemical transformations. PVC, the most common thermoplastic insulation, has a maximum service temperature of 70 °C.
Thermosetting insulation is chemically transformed during extrusion, resulting in a more stable compound in the face of increased temperature. This is why they allow for higher operating temperatures.
The most common thermosetting insulation materials (XLPE and EPR) have maximum operating temperatures of 90 °C.
The higher the maximum operating temperature of an insulation, the more current the conductor can carry. And the more current, the more power it will have. This is the main advantage of thermosetting insulation over thermoplastics.
3. SCREENS OR ARMOUR: CABLE METAL PROTECTION
The third parts of an electrical cable that determines the construction of an electrical cable is the shield or armour.
3.1 SCREEN FUNCTION
In some cases the cables may have metal protections. Electrical metal shields (screens) are applied to isolate the signals that pass through the interior of the cable from possible external interference. Mechanical protections (armours) protect the cable from possible external aggressions..
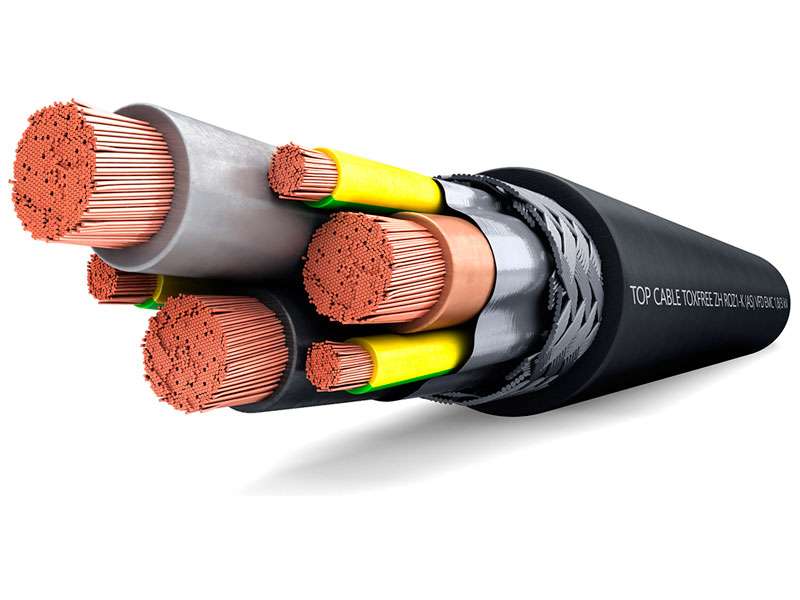
3.2 WHEN SHOULD SCREENED CABLES BE USED?
Screened cables reduce and insulate the transfer of data or power from ‘electrical noise’ or ambient electromagnetic interference (EMI) found in industrial, engineering, or manufacturing environments where a high degree of electrical power is present.
Electric motors, switches, and cables used for energy transmission cause electromagnetic interference (EMI), which can negatively influence data cables, sensors, and similar equipment.
3.3 HOW ARE SCREENED POWER AND CONTROL CABLES CONSTRUCTED?
These parts of an electrical cable again offer different options that define the resulting cable model.. There are different screening types for power and control cables
TIN-PLANTED COOPER BRAIDING
A common method of screening cables is braided copper between the cores and the sheaths. With a degree of coverage of around 80%, the copper braiding forms an effective barrier against electromagnetic fields.
COOPER WIRE WRAPPING
Copper wire wrapping is often used to move cables in robotics, where the screening must withstand torsion. As the copper wires in a wrapping are all positioned parallel to each other, there is no problem with the cable torsion. However, the protection against electromagnetic interference from wrapped cables is often worse as the shield wires do not overlap.
ALUMINIUM-LAMINATED PLASTIC FOIL
Individual cores or all cores in the cable can be wrapped with laminated aluminium plastic foil. The plastic foil screening protects your cables and wires, especially at higher frequencies.
4. CABLE OUTER SHEATH
In almost all cases, an outer sheath is located between the parts of an electric cable to protect it. They are usually made of polymeric material and must be chosen in accordance with the nature of the insulation material.
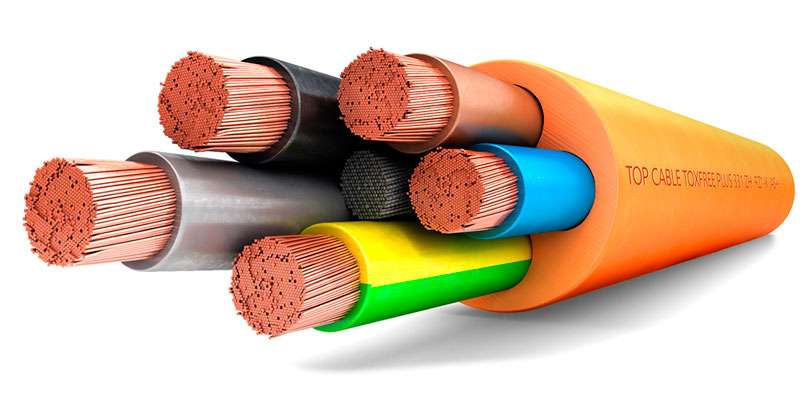
5. COATING MATERIALS
The fifth and last parts of an electrical cable that we want to analyse is the sheathing, which is designed with different materials that dictate the application characteristics..
5.1 WHAT ARE PVC CABLES AND WHEN ARE THEY USED?
PVC cables are very common, are made of polyvinichloride and are applied in machine tools, assembly lines, conveyor systems, production lines and in plant construction, devices and equipment for communication technology, household appliances, generator, transformer and machine construction, switchgear and control construction, electrical and data processing, in cleaning devices, the automotive industry, automation technology, press and mould construction, printing and paper machine construction, surface technology, steel production industry, beverage bottling plants, chemical industry, lamp and lighting technology, etc.
5.2 WHAT ARE POLYOLEFIN (PO) CABLES AND WHAT ARE THEIR ADVANTAGES?
Polyolefin cables are designed with a halogen-free, flame-retardant polyolefin thermoplastic insulation compound with low smoke and toxic gas content. They are used, for example, in public areas such as supermarkets, universities, airports, offices, etc. In addition to being halogen-free, the cables used must be flame-retardant and self-extinguishing, must not contribute to the spread of fire, and must not emit fumes or corrosive gases in the event of fire.
5.3 WHAT ARE RUBBER CABLES AND WHAT ARE THEIR ADVANTAGES?
Rubber cables are electrical cables that are sheathed with a rubber or elastomer layer. This rubber coating provides flexibility, durability and resistance to harsh environmental conditions such as high temperatures, chemicals and abrasions.
5.4 WHAT ARE PUR CABLES AND WHAT ARE THEIR ADVANTAGES?
(PUR) cables are polyurethane cables. This material shows a mechanical behaviour similar to rubber at certain temperatures. They are halogen-free, fire resistant and offer increased mechanical and chemical resistance, making these cables suitable for harsh environments.
These parts of an electrical cable are the ones that allow a classification of the cable and dictate its main characteristics, thus allowing a more accurate selection of the ideal cable for each project.
If you want to know which type of cable is suitable for your project or if you have any questions regarding the parts of an electrical cable, please contact our sales team.